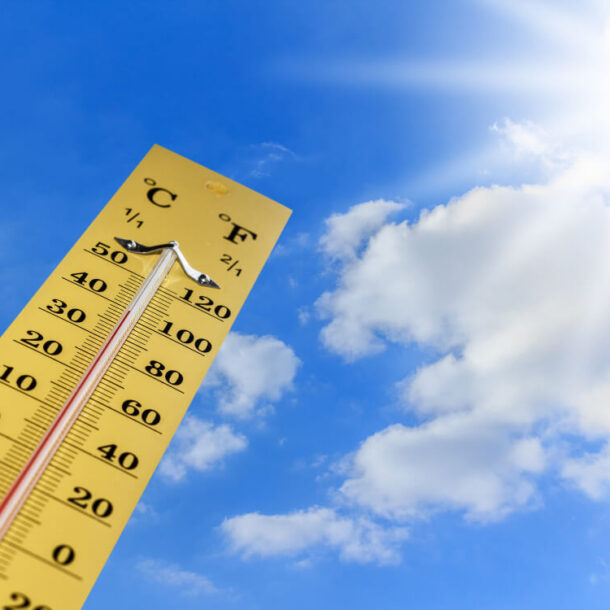
- Solutions
Simplify safety and compliance
- Fuel Saving
- Maintenance savings
- Optimized operations
- Successful temperature-sensitive deliveries
- ELD & DVIR
- Reduced litigations with AI Dashcam
- Variety of automated reports
- Driver scorecard & safe driving reports
- Accident reduction with on-demand & real-time AI video
- Tire pressure safeguarding
- Real-time tracking for theft prevention
- Industries
- Products
- Prices
- Resources
- Company